User Interview
MODEC is Japan’s leading contractor specializing in engineering, procurement, construction, and installation of floating production systems including Floating Production Storage and Offloading (FPSO) vessels, Floating Storage and Offloading (FSO) vessels, Tension Leg Platforms (TLPs), Production Semi-Submersibles, Mobile Offshore Production Units (MOPUs) and other new technologies which will meet the challenges of various types of gas production floaters.
In this interview, we had the opportunity to speak with Mr. Shogo Kawamoto from the Piping Layout Group of the Engineering Department at MODEC. Mr. Kawamoto brings nearly a decade of experience as an FPSO piping engineer, having worked on FPSO construction projects in Brazil and West Africa. He is also an avid user of the advanced 3D CAD software, PlantStream, which he actively employs to optimize operations during the early stages of projects. We delved into how he utilizes PlantStream for FPSOs, which operate in unique environments compared to on-shore plants, and the benefits he has derived from it.
Transforming Past Project Challenges into Future Assets through 3D Modeling: The Significance of PlantStream
Use Case of the Piping Engineering Department in the FPSO Industry
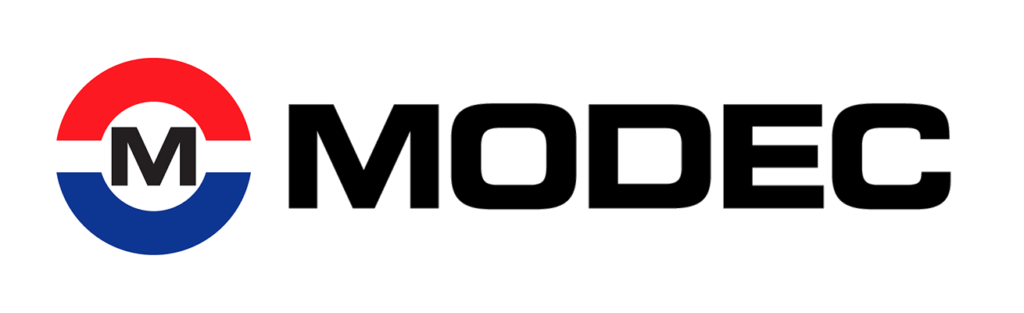
“The FPSO landscape is evolving rapidly, becoming both larger and more complex. To meet customer demands, we sought to streamline our processes with PlantStream.”
– Please tell us about MODEC’s core business and why you chose to employ PlantStream in your project planning.
Kawamoto: To give just a brief explanation of the oil production process at sea: we first anchor the FPSO above the seabed oilfield, using seabed pressure to extract crude oil. This oil is then processed on the FPSO’s topside facility to separate water and associated gas, further purifying it by removing impurities such as sulfur and salt.
The processed oil is stored in tanks within the FPSO’s hull. Periodically, tankers visit to transport the crude oil to land for refining. Notably, the FPSO handles everything from oil extraction to dispatching it to the tankers.
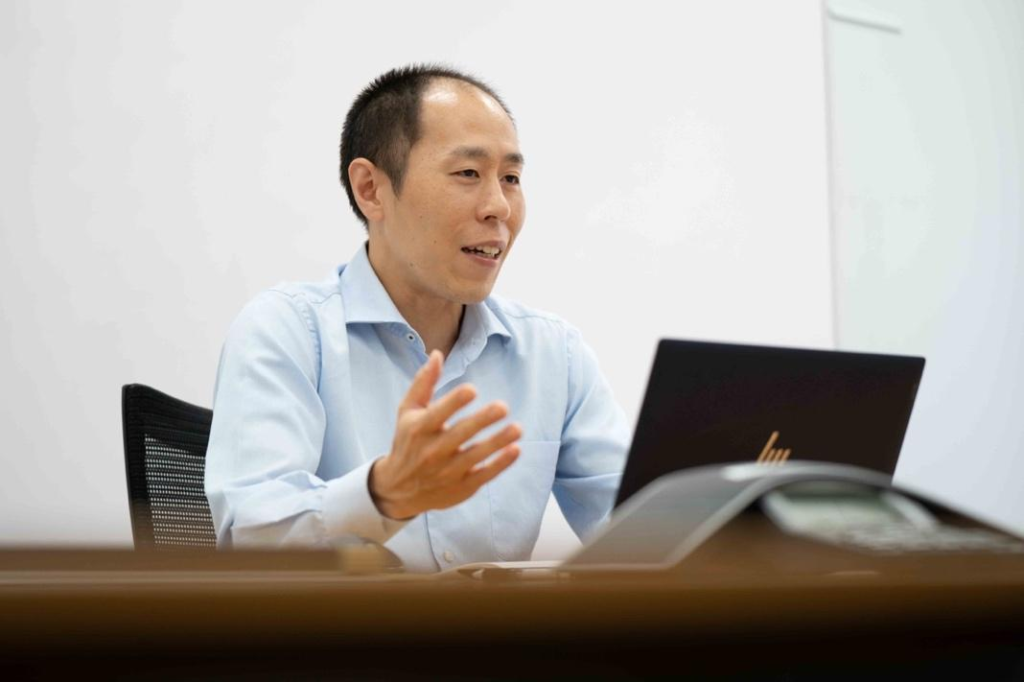
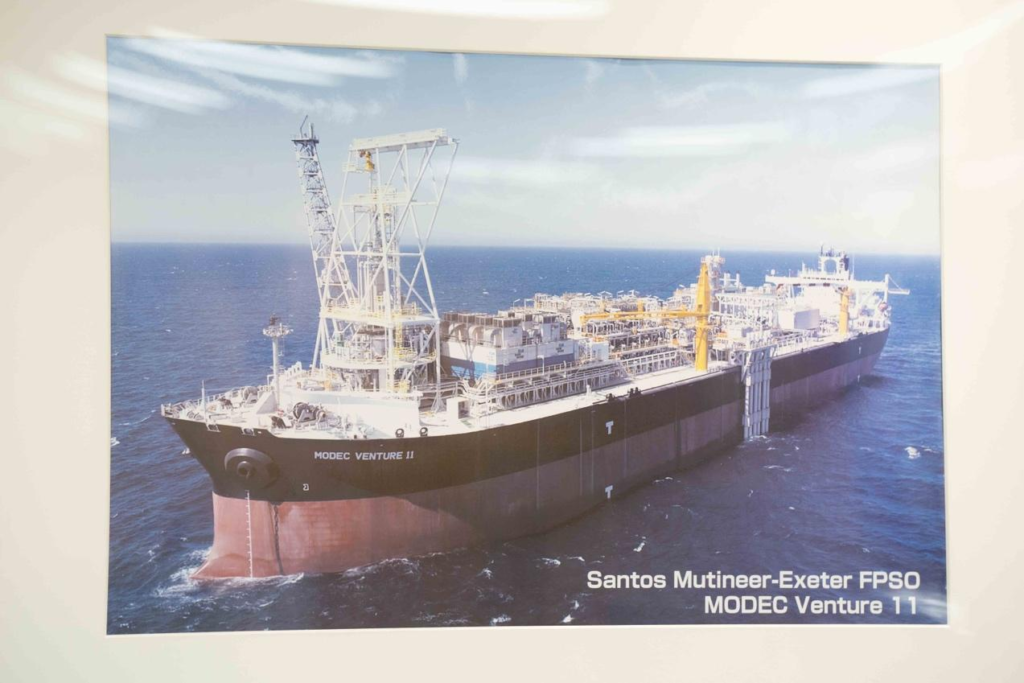
–So, it’s essentially a “large ship equipped with a plant.” Who is your typical clientele?
Kawamoto: Our primary clients are major private and state-owned oil companies. MODEC has developed over 50 floating production facilities, including FPSOs, in regions such as Africa, Oceania, Asia, and Brazil. However, in recent years, the needs of our clients have been evolving, and addressing these changes has become a pressing concern for us.
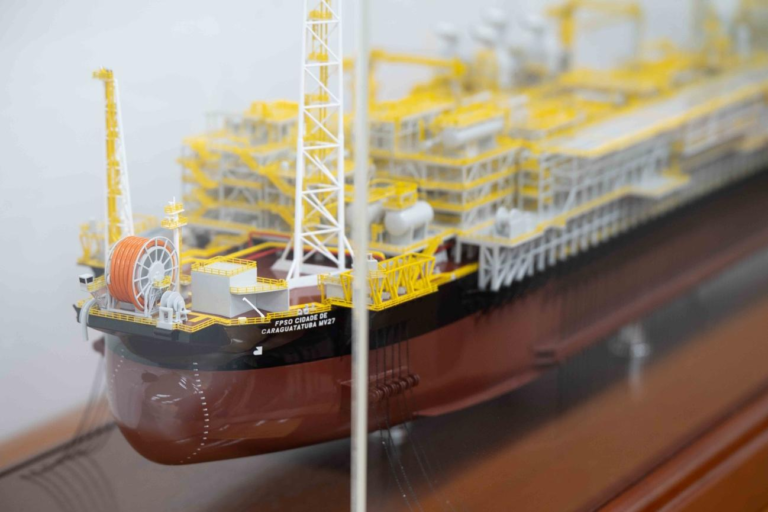
– Could you elaborate on that?
Kawamoto: There is a growing demand from customers for a single FPSO to have a larger extraction capacity and to minimize GHG emissions. This shift demands the construction of even larger FPSOs than before. Piping engineers handling these projects must estimate the required amount of piping and its weight during the FS/FEED phase while accounting for uncertainties along the way. Traditionally, we used past projects as benchmarks and made estimates based on similar plant weights without any actual modeling.
However, with FPSOs now becoming unprecedentedly large and complex, it’s now more difficult for us to rely on past projects as references. This complexity brings unforeseen challenges in safety, profitability, and other areas. This is where the advanced 3D CAD software, PlantStream, comes into play.
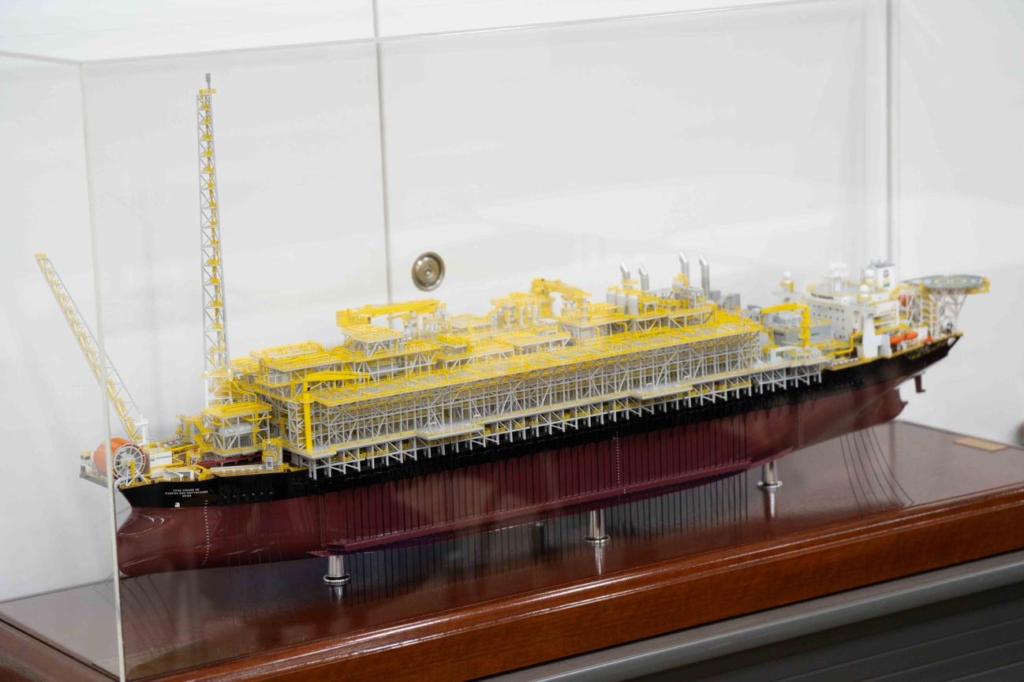
Given the limited weight and space on a shipboard plant, having PlantStream to model the piping layout is very helpful.
– You’ve been using PlantStream for over a year since its implementation. What do you find most appealing about it?
Kawamoto: The largest project we’ve undertaken with PlantStream covers about 10-15% of an FPSO topside. The software automatically routes the piping, and it does so quite rapidly. If we want to model just a few pipes, it’s done in less than a second, which really amazes me.
Additionally, it outputs the necessary information for calculating pipe weight while simultaneously creating a 3D model, which I find to be a significant advantage. An FPSO’s topside consists mainly of elements that can be categorized as machinery, piping, electrical & instrumentation, and structure. Among these, piping accounts for about 25% of the total weight.
In other words, once the piping weight is determined, it becomes clear how much needs to be allocated to structure as well as electrical and instrumentation features. This provides valuable data for other departments, greatly improving weight estimation accuracy. As FPSOs are offshore facilities, they have weight and space constraints that differ from onshore plants. These constraints are quite stringent, so having PlantStream for 3D modeling centered on piping is very helpful for us, and it greatly contributes to the improvement of our estimation accuracy.
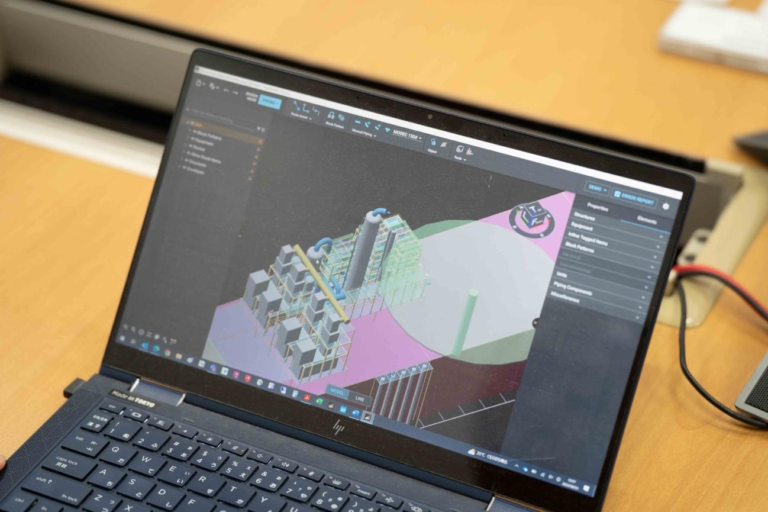
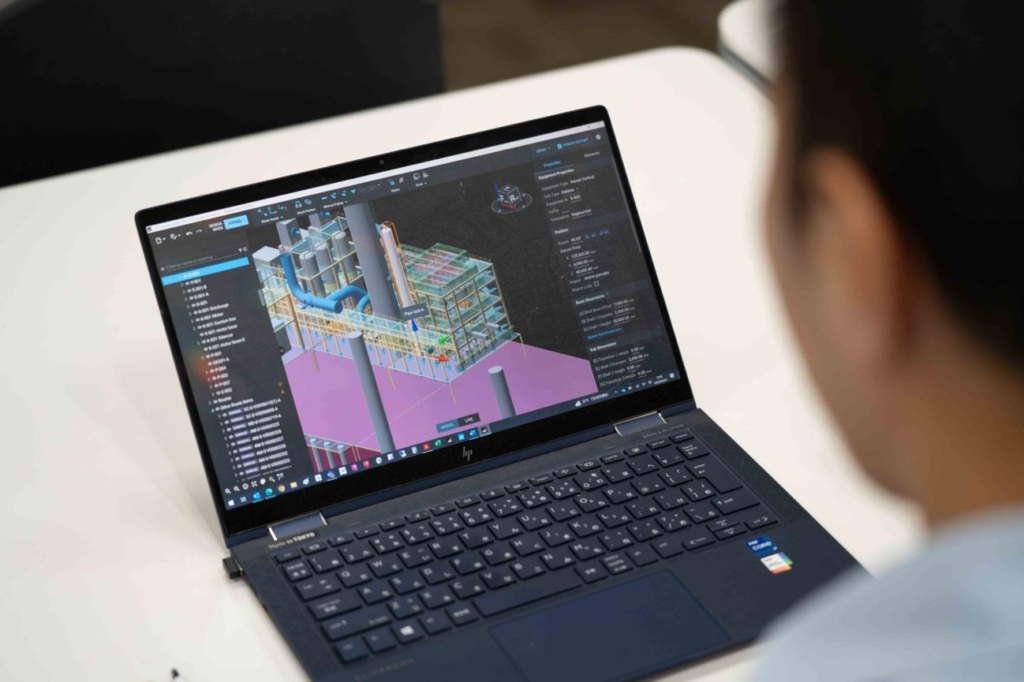
Thanks to 3D modeling, even if there’s a miscalculation, we can refer back to the FS/FEED phase to identify the cause.
– Indeed, constructing a plant on a ship means limited weight and space that requires accurate measurements. Are there any other merits to using PlantStream?
Kawamoto: I would say that it is useful for communication with subcontractors. Typically, after we provide estimates during the FS/FEED and EPC phases, we outsource the modeling to subcontractors. However, with the increasing size and complexity of FPSOs, there are more and more instances where drawings from the subcontractors have differed from our expectations or lacked accuracy/quality. By using PlantStream to first visualize our conception of the FPSO in a 3D model and then sharing that with the subcontractors, we believed it would lead to more accurate model submissions from them.
– The process of creating a 3D model with PlantStream, only to then ask subcontractors to recreate a similar model seems a bit redundant. However, would you say that the advantage of sharing a vision early on makes up for adding extra steps?
Kawamoto: If we were to create this using another 3D CAD software, it would take a long time to become proficient in it, and we wouldn’t have the luxury of relying solely on specialized operators. But with PlantStream, a small team of piping engineers with FPSO expertise can easily create a 3D model. It actually feels more like a streamlining of the process rather than adding extra steps.
Furthermore, if we accurately model in 3D during the initial FS/FEED phase, even if discrepancies arise in weight, quantity, or layout once the actual project starts, we can easily retrace our steps to identify where and why the oversight occurred. The software’s precise verification allows us to make targeted corrections for the current project and enhances accuracy for future projects. This gives us the power to transform past challenges and areas of improvement into future values and assets. This was a major reason for wanting to integrate PlantStream into our processes.
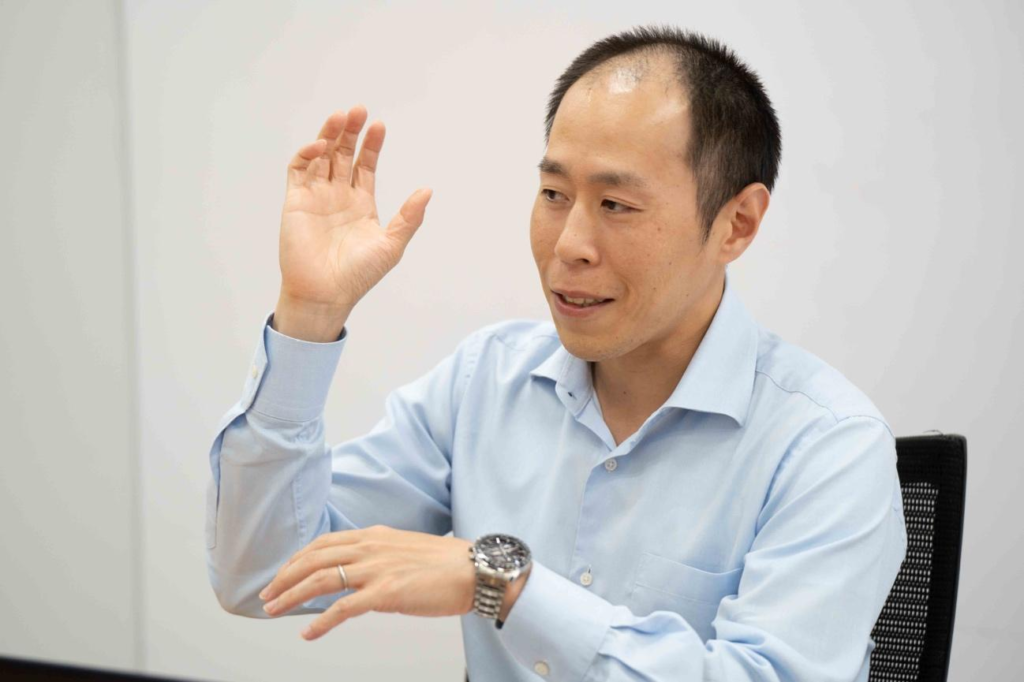
PlantStream facilitates the exchange of ideas between departments and more effective communication of project details.
– It seems that you have become quite proficient in using PlantStream.
Kawamoto: I sure have! It’s been fun getting to know how to use PlantStream. Its intuitive interface allows me to swiftly bring my ideas to life, which is genuinely exciting to me as an engineer.
Especially at the beginning of a project, when there’s nothing tangible yet, visualizing things helps me clarify and organize my thoughts.
Beyond its effectiveness in external communications, PlantStream also plays a pivotal role internally. It facilitates the exchange of ideas between departments and more effective communication of project details.
Once I create a 3D model in PlantStream, I can then simply share that data or just show the modeled screen to other team members, making it easy for them to grasp the piping layout, number, weight, and more at a glance. They can even annotate the 3D models if needed!
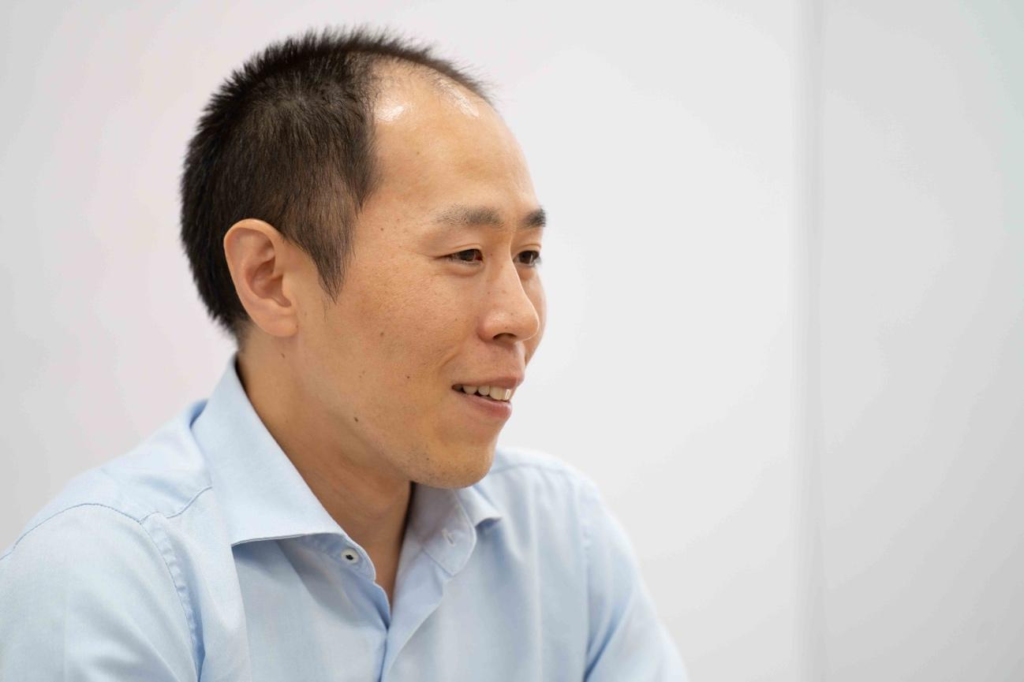
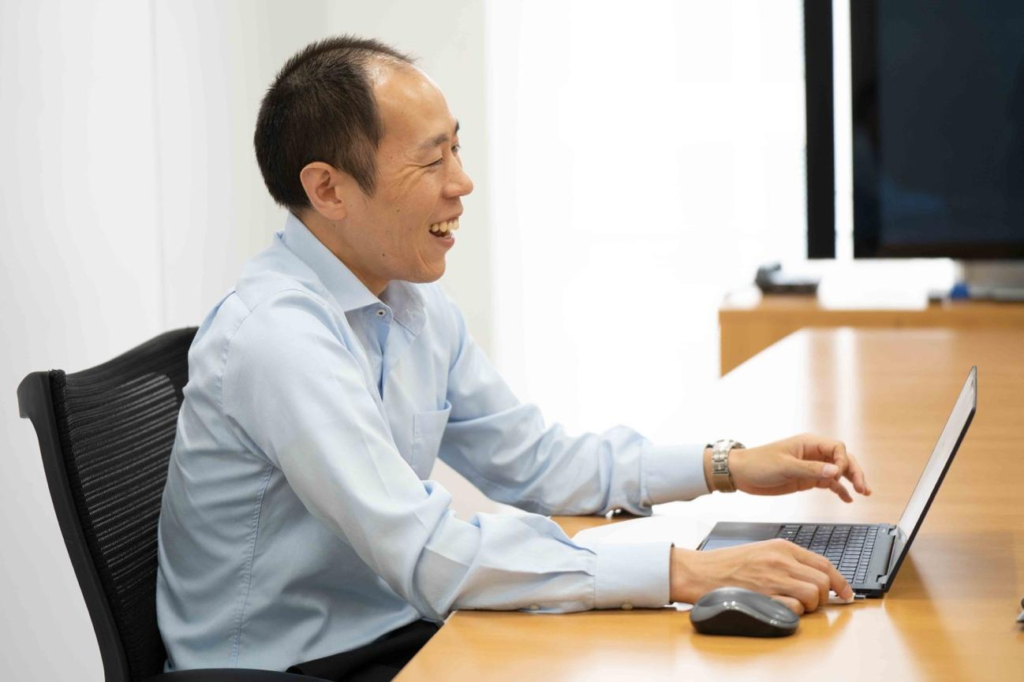
In the past, we only shared basic 2D piping routes or rudimentary Excel sheets. This often left engineers from structures, electrical, or instrumentation teams without much to comment on – typically, our conversations wouldn’t go beyond simple acknowledgments like “I see” or “Understood.”
However, with the visual sharing capabilities of PlantStream, our communication has become more fluid and efficient. We’re able to have more in-depth and qualitative discussions, an unexpected benefit we have experienced post-adoption. Now, there’s a positive shift in the approach of other departments as well. They often ask, “Can you first create it in 3D?” or “I’d like to get an initial 3D visualization.” It’s clear that not only our team but also other departments feel that PlantStream has lowered the barrier to considering things in 3D.
– Finally, could you tell us about your expectations from PlantStream?
Kawamoto: As I mentioned before, our primary field/area of operations at MODEC is the ocean. We have a responsibility to build facilities that can withstand high waves, storms, temperature variations, salt damage, sways, and other marine challenges.
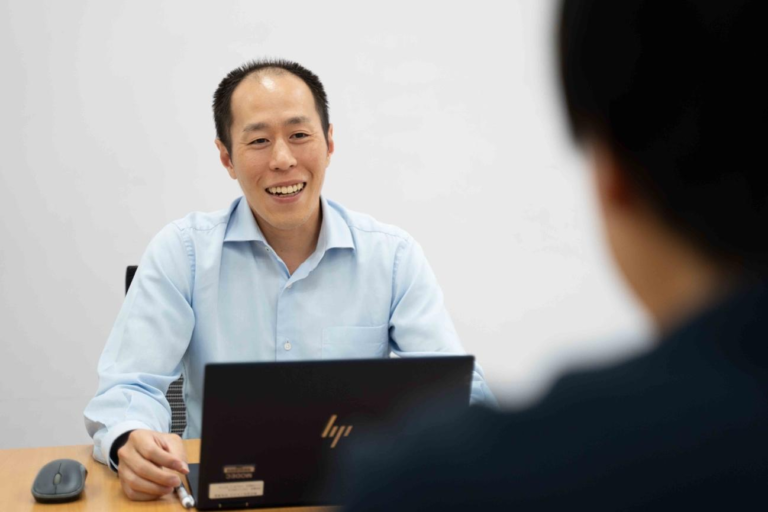
While we greatly appreciate PlantStream, it would be even more beneficial if it considered marine-specific environments or automated piping routing typical to FPSOs. Of course, we also intend to share our insights and expertise with the PlantStream company directly, as we hope to contribute to the software’s updates and improvements.
おすすめインタビュー記事
Book a Demo Today
Connect with an expert to start your PlantStream journey.
Realize more efficient 3D plant design through seamless workflows.