User Interview
Paul Wurth Italy-SMS group (hereafter SMS Paul Wurth), an engineering company for iron and steel based in Luxembourg and Italy, operates in approximately 20 countries worldwide as part of the SMS Group, a leading global company in the steel and non-ferrous metal equipment industry. In this interview, we spoke with Mr. Francesco Scariti, the head of the Plant Design Department, to discuss the challenges that led to the adoption of PlantStream and the results achieved after its implementation.
Challenges:
- Conceptual study in 2D had limitations in accuracy and resulted in a lot of waste of material and rework.
- Multiple layout studies required extensive work.
- Flexible design changes with 3D models.
- Standardization around equipment using the block pattern feature.
- Easy comparison of multiple layouts through material takeoff (MTO).
- Efficient creation of high-precision conceptual study.
- Reduction in man-hours for piping rerouting through equipment layout revisions.
- Significant reduction in material quantity through optimal layout selection.
Paul Wurth Italy-SMS Group’s Success Story: Accelerate Engineering Design Workflow and Boost Competitiveness with PlantStream
Use Case of Design Department at EPC Contractor
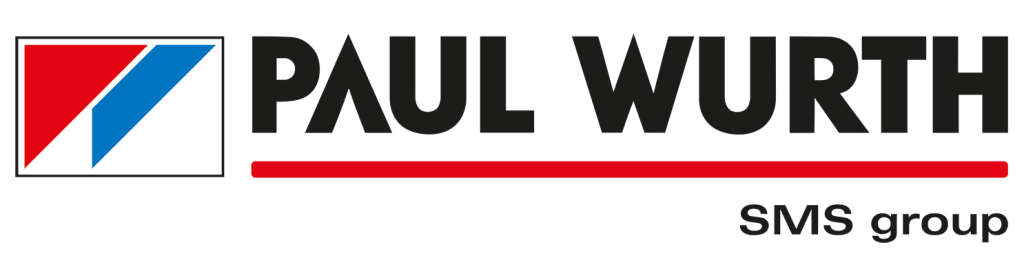
-Could you please share with us your responsibilities and the distinctive aspects of plant design work at SMS Paul Wurth?
As the head of the department responsible for overall plant design and layout study, I oversee various specialized units such as piping, equipment, electrical, and civil engineering. Designing a steel plant requires fitting various facilities into limited space, so we need to be flexible in addressing layout study and design changes.
– What were the challenges you were facing before the introduction of PlantStream?
It’s crucial to present a high-precision conceptual study to clients and subcontractors quickly. However, we used to work with 2D drawings, which made it challenging to identify clashes, resulted in a waste of material, and led to a lot of rework.
Additionally, for steel plant projects, we need to evaluate multiple layouts to find the optimal configuration. However, every time we reevaluated the equipment placement, we had to remodel all the connecting piping and calculate material quantities, leading to a significant amount of work.
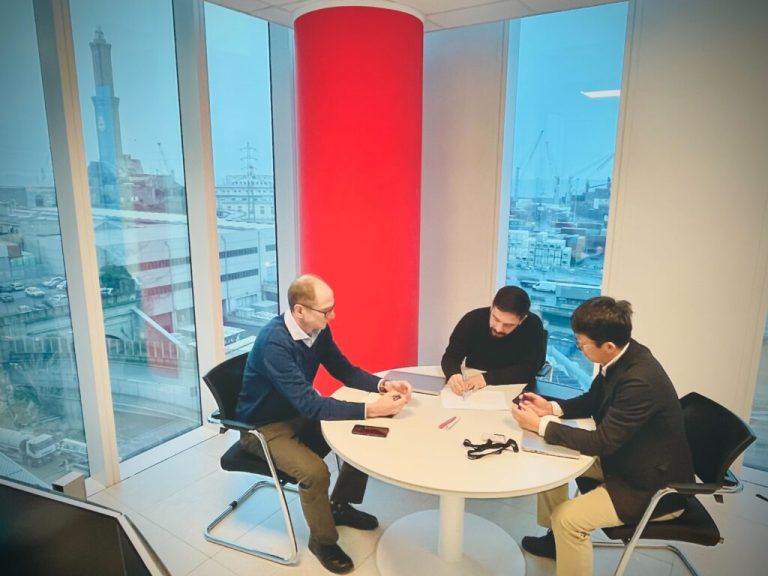
-How has the introduction of PlantStream impacted your work?
We standardized the equipment surroundings utilizing PlantStream’s block pattern feature. Then, we conducted layout studies for each unit and performed piping routing automatically. This allowed us to create multiple highly accurate 3D models in just a few weeks and made it much easier for us to compare different design options.
Compared to the conventional 2D design approach, our design precision and speed have significantly improved, and we now have the flexibility to make design changes in 3D models, which is extremely valuable.
Let me share an example from when we designed the gas treatment plant of the steel plant. At this time, we needed to rearrange the placement of the heat exchanger. However, by using PlantStream, we were able to create a new 3D model of the revised layout in just a few minutes.
Not only that, but it automatically rerouted all the piping connected to the heat exchangers and calculated material quantities for comparison between two different layout options. This resulted in a substantial reduction of approximately 10 tons of materials.
Just like this, PlantStream has significantly contributed to enhancing our competitiveness during the initial design estimation phase. To be honest, we didn’t expect it to be this capable.
-How do you envision the future of SMS Paul Wurth’s digital transformation (DX) using PlantStream, and what are your expectations for PlantStream moving forward?
With the powerful digital tool, PlantStream, we are now able to create 3D models in a very short time, providing high value to our customers. In the future, we plan to expand our use of PlantStream not only in traditional steel plants but also in new business areas for us, such as green steel and hydrogen-related plants. We have high expectations for PlantStream, hoping it can achieve more advanced functions like quantity calculation for civil and structural elements and proposing equipment layouts. As PlantStream continues to evolve, we’re dedicated to pursuing further innovation and enhancing the value we provide to our customers.
Recommended Interviews
Book a Demo Today
Connect with an expert to start your PlantStream journey.
Realize more efficient 3D plant design through seamless workflows.